Nozzle Hole Cutting
Tru-Cut saves us time overall. It prevents us from making mistakes and is more efficient, too. It gives us more of a competitive edge.
— Leadman at a Tank & Vessel Fabricator
Tru-Cut is helpful on your body. Grinding takes a while and hurts your body. Tru-Cut is faster and more efficient, 10 times faster.
— Welder and Grinder at a Tank & Vessel Fabricator
With Tru-Cut, the bevels are clean, speeding things up on our end. The cuts are great and slick — we don’t have to lay out the head at all, and it saves QA time to check things over.
— Shop Lead at an Industry-Leading Tank & Vessel Fabricator
Even Faster Fit-Up
For more than a century, Brighton’s heads have been associated with faster, easier fit-up thanks to our signature Tru-Edge bevel.
The next evolution of our industry’s best head fabrication is pre-cut nozzle holes to save manual labor, eliminate costly mistakes, and increase your project profitability. We deliver a more finished product, you get your project through the shop faster.

Revolutionizing Nozzle Hole Cutting for Improved Efficiency and Precision
Nozzle hole cutting refers to the process of creating precise, circular openings in tank heads. These openings are crucial for installing essential components like inlets, outlets, and instrumentation. Traditionally, this process was performed manually, leading to potential inconsistencies and inefficiencies.
Innovative Technology for Precision Cutting
Tru-Cut 3D is a revolutionary approach to nozzle hole cutting that leverages advanced technology to deliver exceptional accuracy and efficiency. Here’s how it works:
- 3D Scanning and Automatic Adjustment: Tru-Cut 3D begins by generating a precise 3D map of the tank head. This scan identifies any deviations from the theoretical model. It automatically adjusts the cutting path to ensure a perfect fit on the “as-built” head, eliminating the need for manual adjustments.
- High-Definition Plasma Cutting: Tru-Cut 3D utilizes a high-definition plasma cutter to create clean and consistent cuts. This ensures optimal shape and quality for seamless nozzle installation and welding.
- Automated Etching and Beveling: The system can also etch layout points and pad locations onto the head, eliminating manual layout tasks. Additionally, Tru-Cut 3D offers both static and volumetric 3D beveling options, enhancing weld quality and efficiency.
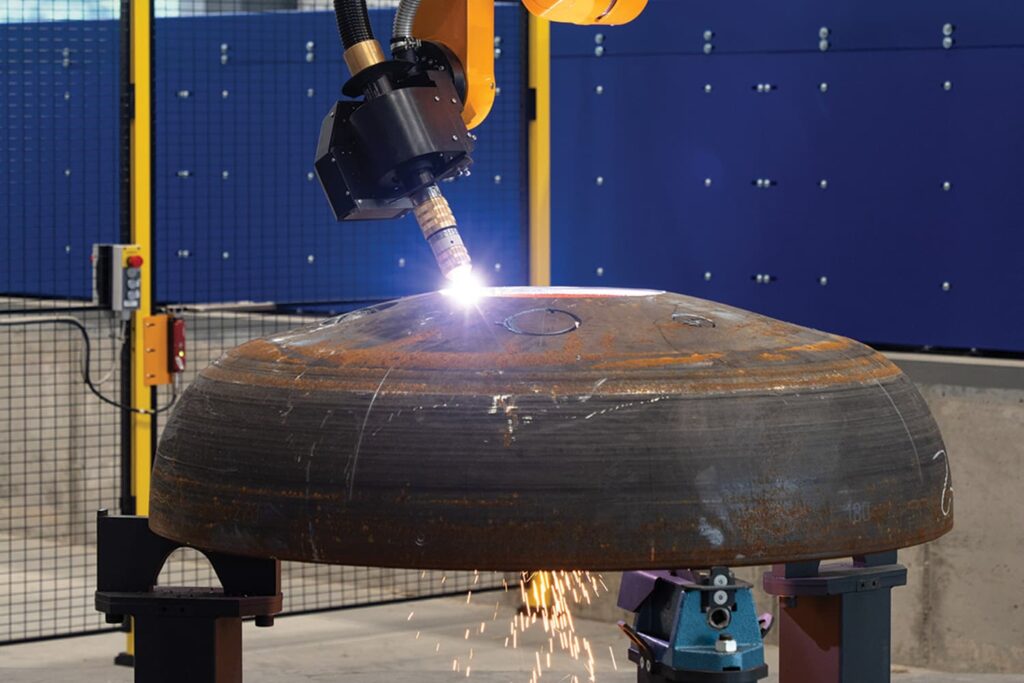
Benefits of Tru-Cut 3D:
- Unmatched Precision: +/- 0.125″ tolerance on location and size, approaching 1/16″ accuracy.
- Faster Fit-Up: High-definition plasma cutting and precise dimensions ensure faster and easier nozzle installation.
- Reduced Manual Labor: Automation eliminates tedious manual tasks, freeing up skilled personnel for other critical fabrication activities.
- Cost-Effectiveness: Tru-Cut 3D offers potential cost savings through reduced labor, fewer mistakes, and faster project completion.
- Minimized Risk: Automatic cutting eliminates the risk of human error associated with manual measurements and cutting.
- Enhanced Weld Quality: Precise beveling options improve weld integrity and efficiency.
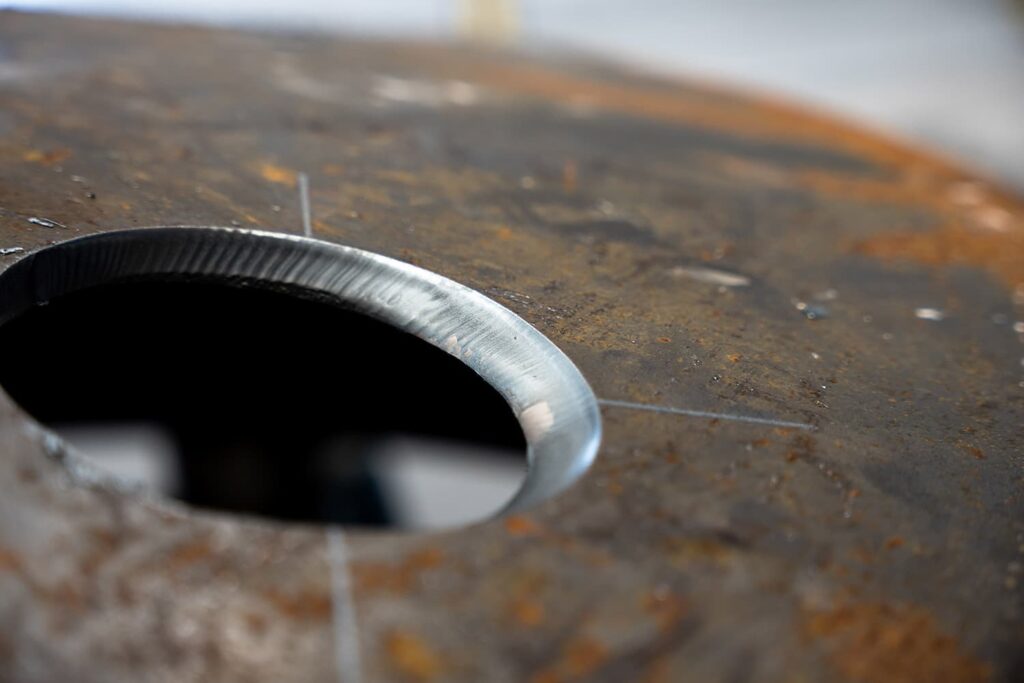
Tru-Cut 3D vs. Traditional Methods: Why Choose the Future of Nozzle Hole Cutting?
Tru-Cut 3D surpasses traditional methods by offering:
- Superior Accuracy: Automated adjustments based on 3D scans guarantee unmatched precision.
- Increased Efficiency: Automation eliminates manual tasks and reduces setup time.
- Reduced Risk of Errors: Automatic cutting minimizes human error and potential rework.
- Improved Cost-Effectiveness: Potential cost savings through faster completion and reduced rework.
7-Axis Mapping: The Secret Behind Exceptional Precision
Tru-Cut 3D leverages the power of 7-axis mapping, providing several advantages:
- Unmatched Flexibility: Reaches complex angles and positions for intricate cuts.
- Enhanced Precision: Finer control over the cutting tool for exceptional accuracy.
- Reduced Setup Time: Performs multiple operations in one setup, saving time and resources.
- Superior Surface Finish: Enables smoother cuts and better finishes, especially for intricate shapes.
- Complex Geometry Handling: Ideal for machining intricate components like turbine blades and impellers.
7-Axis Mapping and Cutting
Tru-Cut 3D achieves exceptional precision thanks to laser scanning and 7-axis cutting capability.
Holes are placed exactly according to the drawings as the cutting head adjusts according to the laser-tracked contours of the head.
Streamline Your Process
Eliminate the measurement, layout, and cutting steps that typically eat up a lot of your shop fabricators time. Heads arrive ready for assembly with pre-cut penetrations and any prescribed etchings complete to aid fabrication.
Custom Beveling
The high level of mobility and precision of Brighton Tru-Cut 3D enables us not only to pre-cut holes, but also to bevel those holes according to your specifications.
Beveling lends to cleaner welds that satisfy your demand for quality.
Eliminate Costly Mistakes
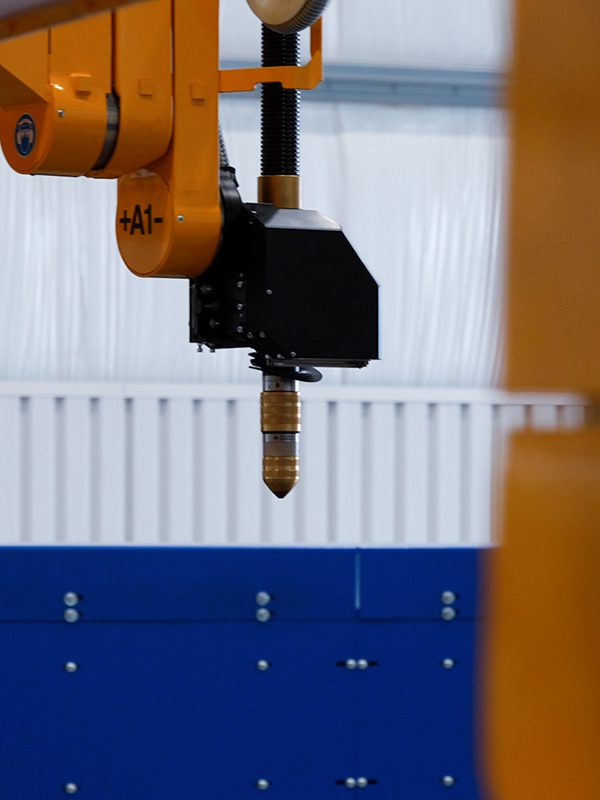
Getting Started with
