Resources
Transportation
In addition to closed truck shipping, we utilize specially designed racks that make it possible for us to transport heads up to 15′ in diameter without oversized load requirements. We also have experience with transporting larger heads, when necessary.
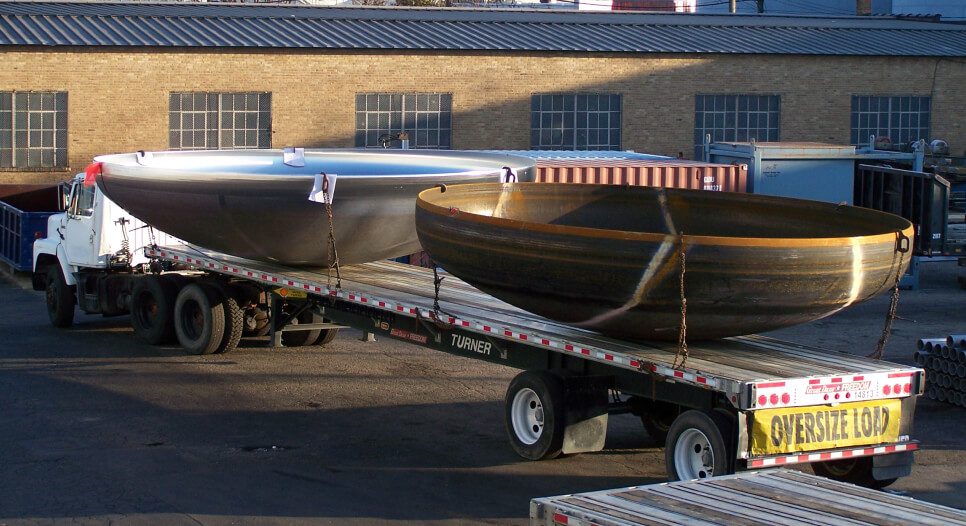
Tank Head Circumference
Circumference Chart
IDD & Volume Charts
Glossary
Fiber elongation of formed heads often requires stress relieving after cold forming of the heads. The stress relieving time and temperatures are outlined in UCS 56 of the ASME Section VIII Div 1 Code. The formula for calculating the fiber elongation is located in ASME Section VIII Div 1 UCS-79.
For heads the calculation is: 75t/Rf ( 1-(Rf/Ro))
t = nom. thickness
Rf = Inside Corner Radius (ICR)
Ro = Dish Radius (infinity for flat flanged only)
MIG
This semi-automatic welding process utilizes an arc between a continuous wire electrode and the weld pool. Shielding is supplied by an inert gas, which flows around the wire through a gas cup attached to the torch.
TIG
This process can be either manual or mechanized. An arc is established between the top of a tungsten electrode and the work piece. The base metal and filler metal are melted, but not the tungsten. A shielding gas flows around the tungsten through a gas cup.
A type of heat transfer surface. Brighton can supply half-pipe for heads and shells.
Heating metal heads to suitable temperatures, holding the part at the temperature for a specific length of time and cooling at a rate to obtain desired mechanical properties and microstructure. Heating for the sole purpose of hot forming is excluded from this definition. However, heating to achieve both forming and heat treatment can be simultaneous under some conditions.
Any metal forming operation that is performed above a metal’s recrystallization (process where new grain structures are formed) temperature.
A nitric acid solution process that removes specific surface defects and contaminants such as iron or scale.
In this mechanized or automatic welding process, a small flow of gas is supplied through the nozzle and its constricting orifice to form a plasma arc. Shielding gas flows through an outer nozzle assembly.
This process uses specialized machining to finish stainless steel products to meet customers’ specifications. Brighton offers mechanical finish on plate, shells, and heads from a #3 to a #8.
Stick Welding
In this manual welding process, an electrode arc is formed between a consumable electrode and the base material. The electrode is covered by a coating that decomposes and melts during welding. This provides a protective atmosphere around the weld area and forms a slag over the weld pool.
Sub-arc
This mechanized or automatic welding process utilizes a blanket of granular flux to protect the weld pool from the atmosphere. A wire electrode is continuously fed from a spool by a wire-feed system. This provide high deposition rates and high heat input.
Materials
Contact us to discuss capabilities for any material you don’t see listed here.
- A572-50
- SA 203-A
- SA 203-B
- SA 203-D
- SA 203-E
- SA 240-C
- SA 285-C
- SA 36
- SA 387- 5-1
- SA 387-5-2
- SA 387-9-1
- SA 387-9-2
- SA 387-11-1
- SA 387-11-2
- SA 387-11-22
- SA 387-12-1
- SA 387-12-2
- SA 387-22-1
- SA 387-22-2
- SA 414-G
- SA 515-55
- SA 515-60
- SA 515-70
- SA 516-60
- SA 516-60N
- SA 516-60N HIC
- SA 516-65
- SA 516-65N
- SA 516-65N HIC
- SA 516-70
- SA 516-70N
- SA 516-70N HIC
- SA 537-1
- SA 537-2
- SA 553
- SA 588,CORTEN
- SA 612
- AAR TC 128-B
- SA 240,304
- SA 240,304H
- SA 240, 304L
- SA 240, 304/L
- SA 240,309S
- SA 240, 310S
- SA 240,316
- SA 240,316H
- SA 240,316L
- SA 240,316/L
- SA 240,317L
- SA 240, 321
- SB 536,330
- SA 240,347
- SA 240,410S
- SA 240, 2101
- SA 240, 2205
- SA 240, 2304
- SA 240, 2507
- SB 127,400
- SB 162, 200
- SB 162, 201
- SB 168, 600
- SB 168,601
- SA 240,254SMO
- SA 240, Ferralium
- SB 333,B2
- SB 333, B3
- SB 409,800
- SB 409,800H
- SB 409, 800HT
- SB 424,825
- SB 435, X
- SB 443, 625
- SB 463, 20
- SB 575, C4
- SB 575,C22
- SB 575,C276
- SB 575, C2000
- SB 582, G30
- SB 625, 904L
- SB 688,AL6XN
- SB 688, 25-6HN
- SB 209,3003-O
- SB 209, 5083-O
- SB 209, 6061-O
- SB 171, Aluminum Bronze
- SB 265, Ti Gr 1
- SB 265, Ti Gr 2
- SB 265, Ti Gr 3
- SB 265, Ti Gr 4
- SB 265, TI Gr 7
- SB 265, Ti Gr 12
- SB 551,702
- SB 551,705
- Specify Backer Thickness
- Specify Cladding Thickness