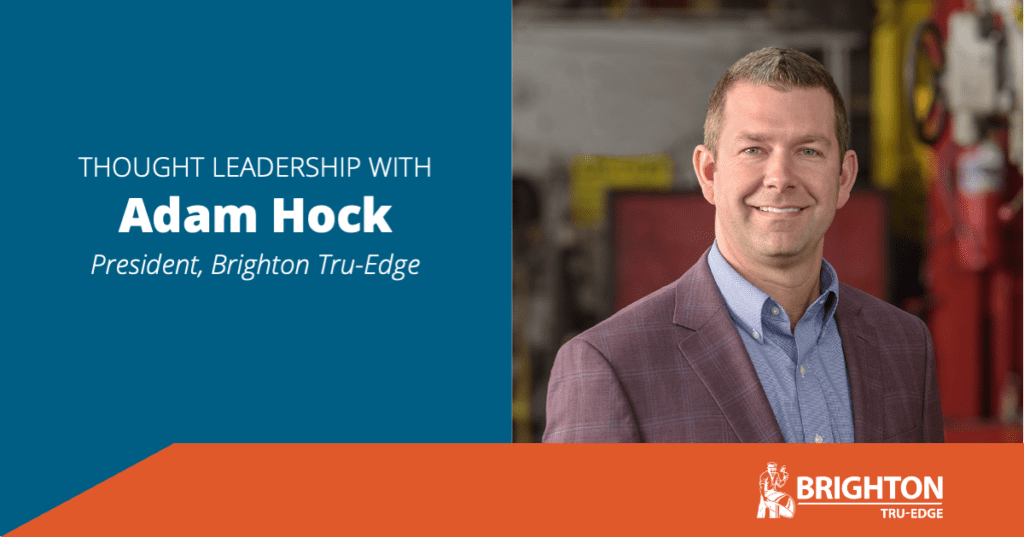
Over the past few years in my leadership role at Brighton, I have had the opportunity to visit many fabrication shops and observe how they operate. It has been enlightening.
I found that most companies in the fabrication space are still doing things the way they did 50 years ago. There are good and bad things about that. On one hand, how we have done things in the past has yielded various levels of success. On the other hand, there are always new technologies and ways of working being introduced into the market providing opportunities for us to increase quality, drive efficiencies, and streamline operations.
There isn’t one magic bullet that will shape the future of our industry. It’s a whole bunch of things, and their implications for how the business operates are profound. Technological advances alone will do things like:
- Make fabrication safer and reduce repetitive stress on the body
- Free up operator time for better, higher-impact work
- Create opportunities to strengthen human interaction and relationships
- Boost efficiency and savings for fabrication customers
- Increase market share for organizations that embrace innovation
- And much, much more.
Take a look at just a few examples of technology and ways of working advancements that have helped transform the traditional fabrication industry.
There isn’t one magic bullet that will shape the future of our industry. It's a whole bunch of things, and their implications for how the business operates are profound.
Nozzle Hole Cutting Technology
One perfect example is a new machine that automates nozzle hole cutting on tank heads. Historically, this operation would take a person a week or two to complete without it. This new machine now does it in a fraction of that time, and the biggest pushback within our shop is that the machine will result in the elimination of jobs. Spoiler alert: It won’t! We know that there is a shortage of skilled labor, and we do not intend to run a fabrication facility with just one or two people. Ideally, this new machine will enable us to double the number of people we employ and increase opportunities for our team because the machine has resulted in more business.
See for yourself how it works in this short clip. Our new machine automates nozzle hole cutting on tank heads, saving our customers the need to cut those holes manually. With our machine, we can spare our customers from making costly mistakes and increase their project profitability. The technology leverages a combination of 3D scanning and automatic adjustment, high-definition plasma cutting, and automated etching and beveling.
Let’s take a step back. We deliver tank heads as a product to customers’ fabrication shops. Up until now, customers have manually cut their own nozzle holes. They would manually pull a tape measure around the product. They would take center dimensions, pull the tape measurer out, and drop in a plumb bob. They would use a center punch to create a hole in the tank head. They would then take a handheld plasma cutter and make a cut. It’s mind-boggling that using a plumb bob is still the method of operation in fab shops today, but that is where the industry is.
It’s mind-boggling that using a plumb bob is still the method of operation in fab shops today, but that is where the industry is.
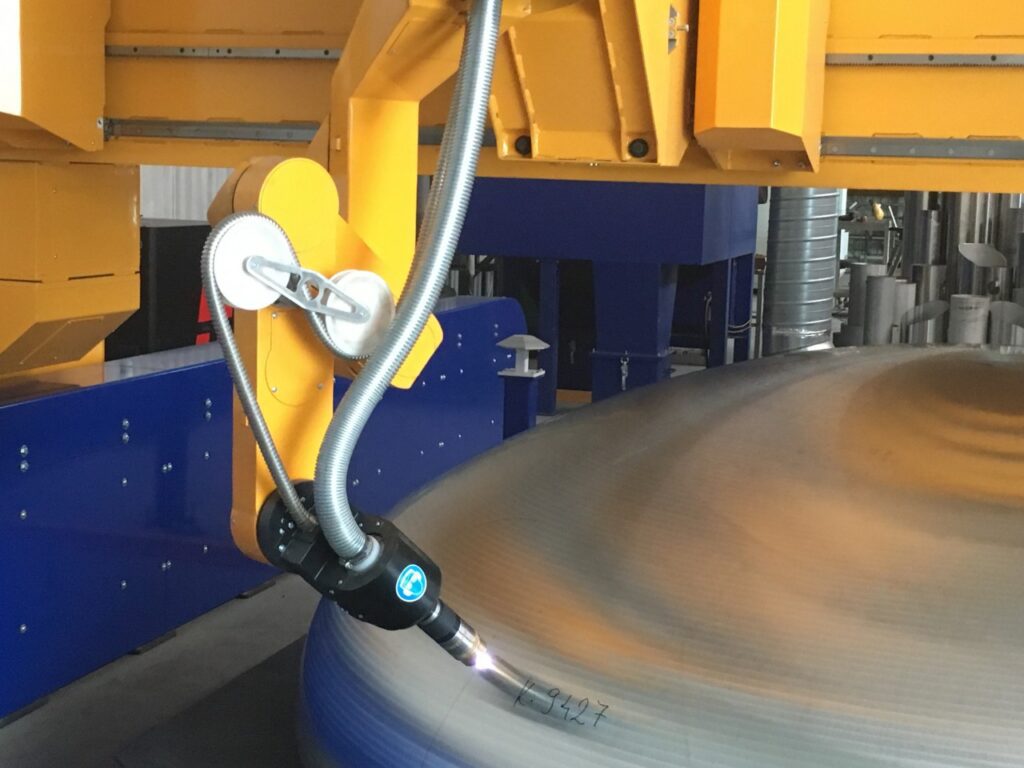
Offering customers the option to purchase tank heads with nozzle holes cut exactly to their specifications is a new idea in the market. Our new machine takes the digital file of what the cuts need to look like, scans the head, and makes the cuts all in one operation. Essentially, it eliminates the need for double handling between our fabricating and the customers’ additional cuts.
The tank head typically arrives at the customer shop at the same lead time, and the customer can start production immediately. This enables the customer to drive more throughput, improve cash flow, and experience fewer errors in the fabrication. The customer is also able to put its talented team members in a position to benefit the organization more.
Think about it — without this new offering from Brighton, the customer has had to put its most talented person on nozzle hole cutting because heads are so expensive that the customer would not want to put a new person on it who might not be as capable of handling it. Now our customers can take that top talent and assign those people work that will help the business do bigger and better things.
This technology is just one example of where our business and the industry are going. Of its size, our machine is the only one in the United States and one of only a few in the entire world. We’ve named ours Tru-Cut 3D.
CNC Programming & Tank Heads
Another advancement of technology that is shaping fabrication’s future is CNC programming. Again, I hear the argument that CNC equipment is eliminating jobs. We will always have the need for skilled employees to run CNC equipment. What CNC has done is increase the productivity of the process. In turn, we are able to reduce the price to the market ensuring increased market share. As we look back on the evolution of tank head forming, we can agree that technology has made life in general better! I can’t imagine making a head with a hammer by manually working metal over a mandrel for 8 hours a day!
With CNC programming, we can now put a head in and have a skilled operator run the machine. The programming memorizes all the motions that the operator ran while making that product. The operator can load the next head, play back the sequence, and create up to about 90% of that product again. This is exciting because it eliminates a lot of the monotony of the operator moving levers and making the products. It also enables a new employee who is less trained to leverage the technology to get up to a more productive level faster. A new employee can learn from watching what the machine is doing. It’s advancing our onboarding and helping this newer level of talent come in and learn faster.
Safety & Reinvesting in Our People
If nothing else, many technological innovations (think robotics in particular) make fabrication safer than the manual way of doing things. Tru-Cut 3D is a good example. In the past, people were lying on their stomachs with a plasma torch blowing molten fire into a metal head to create a hole. In rare cases, a person will attempt to pierce a head with a plasma torch and if the wall thickness is not penetrated, it blows a ball of fire back onto the operator. All these ergonomic risks and safety concerns are eliminated with the new process. In many cases, our shop professionals have said, “Don’t send us another head without holes already cut in it!”
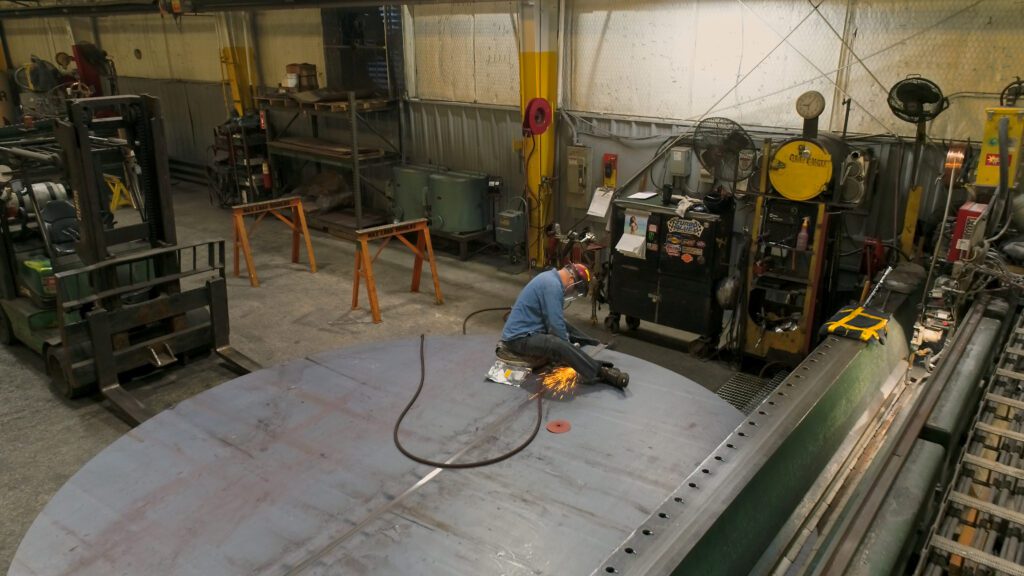
With Tru-Cut 3D, we load a head into a caged cell and close the gates. The cage is outfitted with arc flash protection, fume extraction, gate sensors (to prevent someone from entering while the machine is running), and an elevated workstation to monitor the operation from a safe distance. The level of safety considerations that went into this machine were all engineered into the system to ensure we go without incident. This is all about providing a clean and safe working environment which will enable us to attract and retain top talent.
Tru-Cut 3D even reduces the manual labor that creates a risk for repetitive stress injuries. It eliminates the need to work in physical positions that can cause long-term health problems, and that is important because after keeping a person physically safe, the next step is ensuring they live longer, healthier lives.
Employers have a big impact on employee lifestyle (e.g., healthy eating, regular exercise, stress management, etc.), who in turn pass safety on to their families. It’s cultural. We want to take care of our people. We owe it to them. They are dedicated to our organization, so we owe it to them to help them have as long and as fulfilling of a retirement as they can. After everything they give us, we need to ensure that they can spend quality time with their families.
Employers have a big impact on employee lifestyle (e.g., healthy eating, regular exercise, stress management, etc.), who in turn pass safety on to their families. It’s cultural.
The Future of Fabrication Holds Great Promise
Change can be uncomfortable, especially if we accept the way things are done. As I said, the biggest pushback we’ve received from Tru-Cut 3D is that it will replace folks in their jobs (and again, it won’t). A tough way to present the situation is to say that it’s either kill or be killed, at least to some extent. If we do not innovate and grow, we will be run out of business by others who do. Honestly, though, “because we have to” is not the message I want to emphasize.
Anyone who is uncomfortable or untrusting of these sorts of changes should remember that there must be balance. In taking market share as a result of technological advancements, we want to create more opportunity and stability for our people, which will create longer-term solutions for their kids and their grandkids and opportunities for the future. It’s not about eliminating positions. It’s about growing and creating a more stable, prosperous organization and stability for our people.
So, if you are looking to grow and differentiate yourself, embrace new technologies and ways of working and integrate them into your operations as they make sense. It will transform your business.