Heat Treatment Process
Heat treatment in our oversized furnace — capable of reaching 2000°F — helps meet customers’ code requirements and needs.
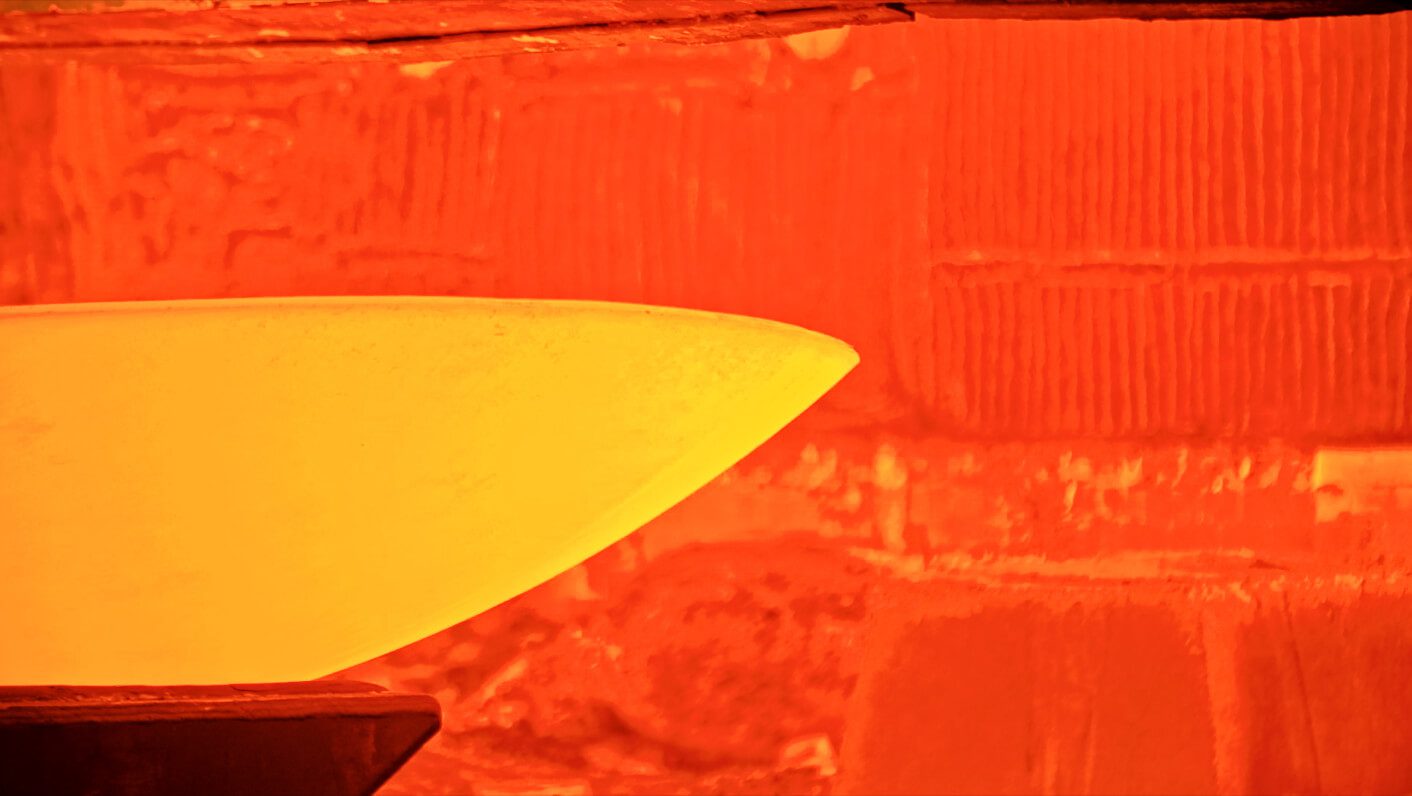
The Tru-Edge Difference
Forge in Fire
Different heat treatment processes helps ensure the quality and performance of our cold-formed heads
Normalizing enables us to heat heads — either in the flat or after forming — into the transformation range.
Stress Relieving alleviates work hardening stresses in the material.
Solution Annealing heats stainless steel and nickel alloys to dissolve carbide and increase corrosion-resistant properties.
Normalizing enables us to heat heads — either in the flat or after forming — into the transformation range.
Stress Relieving alleviates work hardening stresses in the material.
Solution Annealing heats stainless steel and nickel alloys to dissolve carbide and increase corrosion-resistant properties.
Why Heat Treatment?
Putting cold-formed heads through heat treatment helps maintain the strength of the metal to meet code requirements and ensure long-lasting performance.
The Process
Computer-controlled furnace—capable of reaching up to 2000°F—are programmed for the specific needs of a piece to complete the heat treatment cycle. We utilize thermocouples attached to the heads to ensure proper heating of the material.
The Difference
Brighton engineers and metallurgists utilize different heat treatment processes, dependent on the project needs, to achieve the proper performance standards of our heads.
The NEXT EVOLUTION of Tank Head Manufacturing
Tru-Cut 3D Nozzle Hole Cutting
The next evolution of our industry’s best tank head manufacturing is pre-cut nozzle holes to save manual labor, eliminate costly mistakes, and increase your project profitability.